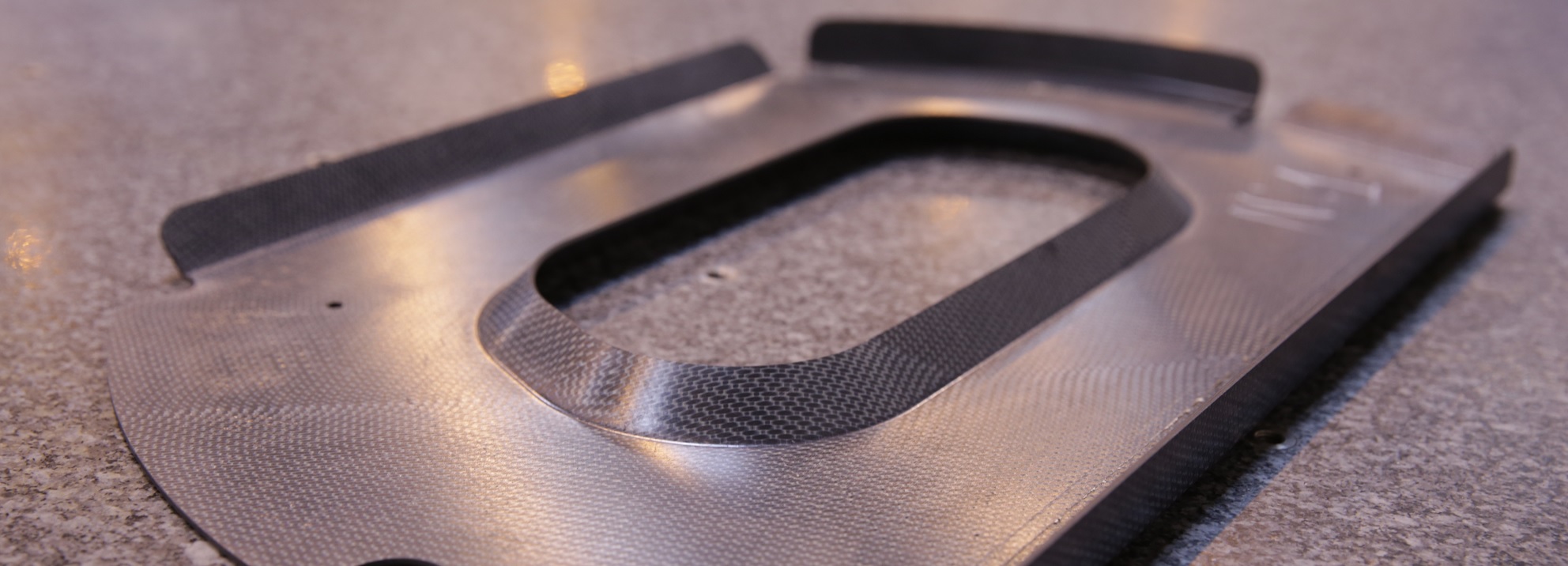
On November 28 and 29, Daher is hosting the SAMPE France (Society for the Advancement of Material and Process Engineering) Technical Days under the banner ‘Emerging Processes for a Green Revolution’. The two-day event provides an excellent opportunity to restate Daher’s leading position in thermoplastics for the aerospace industry, and its current involvement in this sector of the future.
Thermotastic! Thermoplastic (TP) is an innovative aerospace industry material that offers many advantages over other composites, such as thermosets. This material is now a major focus for development at Daher, which has devoted a significant proportion of its R&T budget to this material of the future.
Thermoplastic lends itself more easily to production automation. It’s also a recyclable, repairable and weldable material, whose mechanical properties mean that it can be used in smaller quantities and to make structures lighter overall.
Pierre Rouch, TP Composite Technical Expert at Daher
Jean-Luc Daligault, Head of the Aerostructures Business Line at Daher: “We’re now at a pivotal moment for thermoplastic, which is coming of age and emerging as a real game changer in the world of aerostructures. It allows us to produce lighter, stronger, components than was possible with the metals previously used, and to do so at lower cost and higher speed. Significant performance gains in terms of weight reduction, fuel savings, high-temperature resistance and improved tolerance to damage and stress, together with the opportunity to limit the environmental impact of air transport, explain the enthusiasm for this material in the aerospace industry supply chain. This is the key issue for tomorrow’s aerostructures.” Significantly, Daher has demonstrated a significant lead in this market.
The advantages of being both an aircraft manufacturer and equipment manufacturer
In an environment engaged in a race for innovation that involves the entire value chain in working together collaboratively, Daher’s status as an aircraft manufacturer gives it assets that set it apart from the rest of the field…
Thermoplastic remains a new material we use in an industry where safety is a major challenge… aerospace. Qualification is the central issue. We must be able to demonstrate that the components we design will be able to withstand everything an aircraft experiences without becoming damaged in the process. As an aircraft manufacturer, we have both the qualification/certification mindset and the ability to conduct tests on our own aircraft. That makes us truly unique…
Jean-Luc Daligault, Head of the Aerostructures Business Line at Daher
Nantes: thruput and performance
In terms of TP mass production, Daher is unequivocally the European leader, since its Nantes plant is the largest in the market. “It produces a TP component every 3 minutes,” says Pierre Rouch. “Nantes is THE Daher dedicated site for thermoplastic composites. As such, it benefits from a policy of substantial investment and innovation focused on process automation and the development of high-thruput production capacities. For example, it has one of the few Automatic Fiber Placement (AFP) machines in existence, which optimizes the component fiber placement in three dimensions simultaneously. Dedicated exclusively to R&T projects, this machine allows us to prepare for industrial-scale production of new thermoplastic composite parts within a timeframe of 3 to 5 years.”
The 160,000 components produced by the two automated production lines of this plant every year include moving parts, small ribs, nearly a thousand different types of clip, floor structures and even engine cowls for several major aerospace programs.
Its high-thruput performance and state-of-the-art production resulted in the Daher plant in Nantes being awarded one of France’s very first Vitrine Technologique (Technology Showcase) labels in 2015 by a group of industry organizations, including the French Aerospace Industries Association (GIFAS), which has produced a roadmap for the development of a future European TP sector.

Innovative structures and processes
Daher is now focused on developing thicker components and structural components subject to high stresses. Successful tests already conducted by Daher include the large wing ribs developed two years ago as part of an innovation program led by the French Civil Aviation Research Council (CORAC). “These deliver a weight saving of just over 35% at the same cost as aluminum,” continues Pierre Rouch.
As a partner in the Wings of Tomorrow (WoT) project alongside Airbus, Daher is now responsible for the design and manufacture of five high-load thermoplastic ribs. Now in production, they will be delivered during 2020 for installation in the first full-scale demonstrator.
Following its 2018 acquisition of Dutch startup KVE, which specializes in composites, Daher has been able to introduce a niche TP induction welding technology. This innovative process can potentially reduce the number of rivets and the overall weight of the application concerned by an additional 15%.
So what might the future hold?
Over the coming years, Daher plans to continue its R&T effort in alignment with its product and service strategy and the aerospace industry roadmap. One of its central goals is to improve its ability to recover and process production offcuts and recycle end-of-life TP components; in fact, any TP component that can potentially be processed, repurposed, requalified and reused for new applications. At the same time, and beyond applications in wings, TP is already continuing to expand its applications into many different areas of aircraft construction and maintenance. “In terms of thermoplastics, Daher is currently working on around ten other projects and trials, and all these technological innovations will – of course – one day find their way into our own aircraft,” concludes Pierre Rouch.