Modernste Verbundwerkstoffe für die Luftfahrt: Wie Daher das Feld der Möglichkeiten immens erweitert
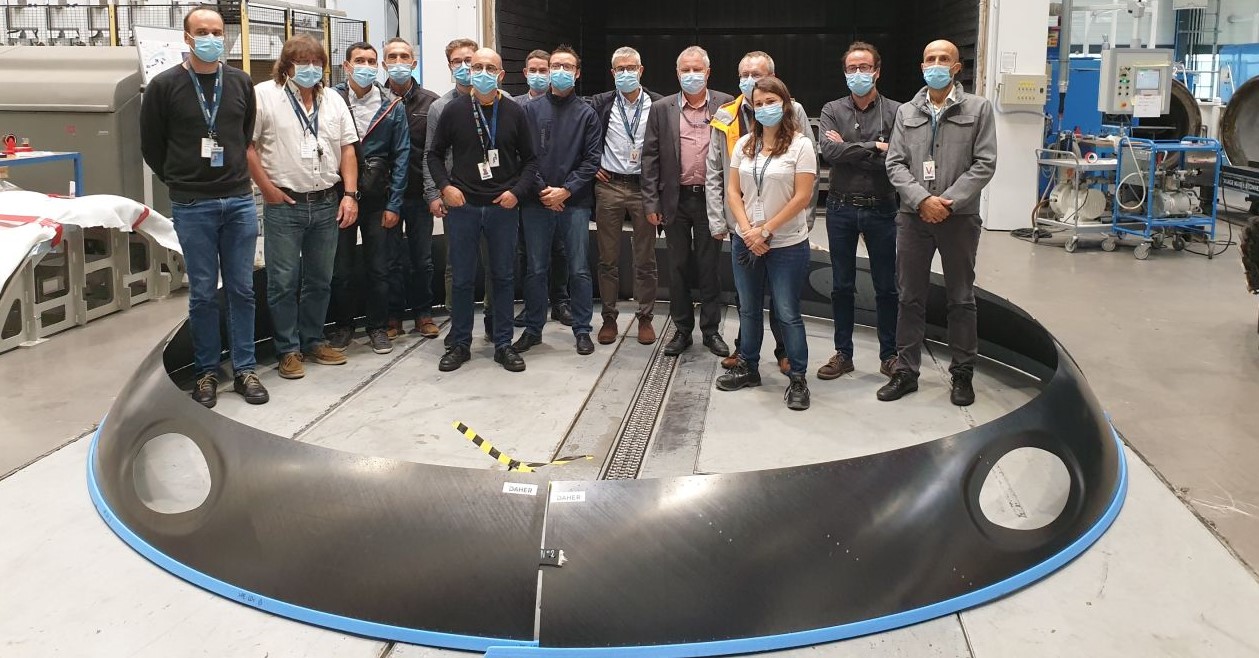
Sind wir in der Lage, Konzeption und Herstellung mit einer Reduzierung unserer Umweltauswirkungen zu vereinbaren?” Die Veranstaltung, die am 26. November zu diesem Thema stattfand, ermöglichte es Daher einmal mehr, seine führende Rolle und die Relevanz seiner langjährigen Strategie im Bereich der Verbundwerkstoffe und modernsten Verfahren für neue, effizientere und umweltverträglichere Anwendungen in der Luftfahrt zu unterstreichen
Die Verbesserung der Aerodynamik und der Ökoeffizienz von Verkehrsflugzeugen steht im Fokus des Airbus-Programms „Wing of tomorrow“, das die Entwicklung einer neuen Generation von Flügeln für Single-Aisle-Flugzeuge (New Single Aisle) zum Ziel hat. Es stehen viele Fragen auf der Tagesordnung: Verkürzung der Time-to-Market, Kostenreduzierung, Leistungssteigerung, Gewichtsreduzierung, Produktionsraten usw. Indem Daher mit der Konstruktion und Fertigung eines Holms aus duroplastischem Verbundwerkstoff und fünf hochbelastbaren thermoplastischen Rippen im Rahmen dieses großen F&E-Projekts beauftragt wurde, wollte Airbus von einem einzigartigen Know-how profitieren, das sich im Laufe der Jahre mit einer systematischen Reihe von F&E-Projekten angesammelt hatte.
„Die Lieferung dieser Rippen 2020 – hochbelastbare, große und komplexe Strukturteile, deren Stärke je nach Zone variiert – ist das Ergebnis der strategischen Entscheidung von Daher vor mehr als zehn Jahren, die F&E-Anstrengungen, die die Transformation der Gruppe begleiten, auf die Entwicklung und Produktion von Verbundwerkstoffteilen mit höherem Mehrwert zu konzentrieren”, erklärt Dominique Bailly, Direktor für Forschung und Entwicklung bei Daher. „Indem wir sehr schnell zwei vorrangige Bereiche – den Flügel und das Triebwerksumfeld – identifiziert und in den Mittelpunkt gestellt haben, konnten wir eine technologische Roadmap erstellen, die es uns ermöglicht, rechtzeitig wettbewerbsfähige und differenzierende Lösungen mit dem richtigen Reifegrad und zu den richtigen Kosten anzubieten, um den Herausforderungen der Luftfahrtindustrie zu begegnen. Jetzt werden die Früchte unserer Bemühungen langsam sichtbar.”
Die Tragflächen: ein schrittweiser Optimierungs-Ansatz
Was die Tragflächen angeht, so zielt Daher auf drei Kategorien von Teilen ab: Holme, Rippen und Torsionskästen. Dabei hat Daher einen entscheidenden Vorteil: Die Eigenschaft als Flugzeughersteller ermöglicht es dem Unternehmen, Innovationen an seinen eigenen Flugzeugen – leichten Maschinen der allgemeinen Luftfahrt – zu entwickeln und zu testen, bevor es sie auf höhere Flugzeugkategorien hochskaliert.
Das erste Großprojekt ist die EcoWingbox, ein großer, 14 Meter langer Flügel aus Kohlefaserverbundwerkstoff, der zwischen 2009 und 2014 für ein Daher-Flugzeugprojekt entwickelt wurde. Für die Aushärtung dieses großen Teils wird der Autoklav durch einen Ofen ersetzt, der die gleiche Produktionskapazität zu wesentlich geringeren Kosten bietet.
„Mit den Investitionskosten für einen Autoklaven können wir fünf Öfen kaufen und so die Herausforderung annehmen, die Produktionsraten der Luftfahrtindustrie zu beschleunigen“, betont Dominique Bailly. Das Verfahren wird daher bei allen künftigen Projekten angewandt werden.
2017 startete Daher zusammen mit Dassault das Corac-Projekt „Das Verbundwerkstoff-Flugzeug der Zukunft”, in dessen Rahmen eine erste thermoplastische Rippe sowie ein hinterer Holm vollständig aus duroplastischem Verbundwerkstoff außerhalb des Autoklaven entwickelt und hergestellt wurden. Die Geschichte geht also weiter, und bei Daher wird die Produktion komplexer Verbundwerkstoffteile immer ausgereifter. Größere Teile, die stärker beansprucht werden, mehr Funktionen integrieren, eine andere Stärke haben usw.”, fasst Dominique Bailly zusammen.
„Dieses Projekt gab uns auch die Möglichkeit, eine erste Rippe aus Thermoplast, dem Schlüsselmaterial für bestimmte Flugzeugstrukturen der Zukunft, zu entwerfen, zu produzieren und in realem Maßstab zu testen, was es uns ermöglicht, zu niedrigen Kosten und mit hoher Produktionsrate Teile herzustellen, die leichter, aber auch widerstandsfähiger sind, als die bisher verwendeten Metalle.”
Seither ist Daher bereit, noch weiter zu gehen, sich noch schwierigeren Aufgaben zu stellen. Dank seines technologischen Vorsprungs konnte das Unternehmen 2019 in das ambitionierte Airbus-Programm „Wing of tomorrow“ aufgenommen werden, in dessen Rahmen es mit der Entwicklung und Herstellung einiger der kritischsten und komplexesten Teile des Programms betraut wurde: einem vollständig aus duroplastischem Verbundwerkstoff außerhalb des Autoklaven gefertigten hinteren Holm sowie den fünf auf der Messe vorgestellten Typen von thermoplastischen Rippen.
„Wir sind sehr stolz darauf, dass wir die hohen Erwartungen von Airbus an dieses Projekt erfüllen konnten und zu den Ersten gehören, die geliefert haben. Dies ist ein weiterer Beweis für unsere Kompetenz auf dem Gebiet moderner Verbundwerkstoffe. Es zeigt auch, dass unsere strategischen Entscheidungen richtig waren: Wir haben bereits 2009 in diese wichtigen Tragflächenteile investiert!”
Daher fügt nun einen neuen Baustein in sein Firmengebäude, das thermoplastische Induktionsschweißen – ohne Nieten -, das eine erhebliche Reduzierung des Gewichts und der Montagezeit des Flugzeugs ermöglicht. „Auch hier nutzen wir unsere Flugzeuge der allgemeinen Luftfahrt, um die Vorzüge dieser Technologie und unsere Fähigkeit, ein kritisches Teil zu entwickeln und zu zertifizieren, zu demonstrieren. Im Rahmen des Corac Trampoline-Projekts arbeiten wir in Forschung und Entwicklung an einem Beispiel für einen Torsionskasten, der mit der festen horizontalen Ebene des Flugzeugs verschweißt ist. Unser Ziel für die Zukunft ist es, diese Technologie bei unseren Kunden und Partnern einzusetzen, indem wir nach der Validierung unserer Entwürfe Tests an den beweglichen Teilen des Flügels oder des Leitwerks größerer Flugzeuge anstreben. Mit unseren Flugzeugen verfügen wir über eine einzigartige ‘Plattform’ für Experimente und Demonstrationen, um die herum wir unser internes Innovationsprogramm aufgebaut haben und deren Vorzüge wir an unsere Partner und insbesondere an andere Flugzeughersteller weitergeben können. Wir sind in der Lage, neue Technologien in kleinem Maßstab zu testen, ihre Zertifizierungsfähigkeit… und sie können sich dann ein „Scale-up“ für ihre eigenen Programme vorstellen. Das gilt auch für die Hersteller von Motoren…”

Der Horizont wird weiter – im Triebwerksbereich
Die Strategie von Daher im Triebwerksbereich nimmt mit der Herstellung eines ersten Strukturteils aus thermoplastischem Kunststoff eine entscheidende Wendung: der Lufteinlassrahmen eines Prototyps des revolutionären UltraFan-Triebwerks von Rolls-Royce. Mit einem Umfang von mehreren Metern ist dieses Teil, das aus 4 zusammengesetzten Sektionen besteht, eines der größten, die jemals aus Thermoplast hergestellt wurden.
Rolls-Royce hat Airbus mit der Entwicklung der Gondeln für dieses Triebwerk einer neuen Generation beauftragt, das den Treibstoffverbrauch um etwa 25 % und die Lärmbelastung bei Langstreckenflugzeugen drastisch senken soll. Der UltraFan wird das größte Flugzeugtriebwerk der Welt sein, wenn es gegen Ende des Jahrzehnts in Betrieb genommen wird. Die Herausforderung für Airbus besteht darin, eine Gondel mit noch nie dagewesenen Abmessungen zu entwickeln, ohne das Flugzeug schwerer zu machen. Der massive Einsatz neuer Verbundwerkstoffe war von entscheidender Bedeutung, und die Wahl von thermoplastischen Kunststoffen für den Lufteinlassrahmen war eine Weltneuheit. Für die Herstellung wandte sich Airbus natürlich an Daher, das bereits am “Wing of Tomorrow”-Programm beteiligt war und seine Fähigkeit zur Herstellung besonders komplexer Teile aus thermoplastischem Kunststoff bereits unter Beweis gestellt hatte.
„Airbus ist für das Design und die Auswahl der Materialien verantwortlich, aber wir haben uns an einem echten Co-Engineering-Ansatz beteiligt, um sicherzustellen, dass das Teil mit der automatisierten Faserplatzierungstechnologie (AFP), die wir als einer der ersten auf dem entsprechenden Niveau beherrschen, hergestellt werden kann – und das zu bezahlbaren Kosten”, erklärt Alexandre Lambert, F&E-Projektleiter bei Daher. „Die Herausforderung war jedoch beträchtlich angesichts der Eigenschaften des Teils, nämlich seiner immensen Größe, seiner sehr geringen Materialstärke und seiner konischen und gekrümmten Form… Eine sehr komplexe Gleichung, die wir jedoch in Übereinstimmung mit den Vorgaben von Airbus lösen konnten. Das Teil wurde für die für 2023 geplanten mechanischen Flugtests zugelassen. Daher ist sehr stolz darauf, thermoplastische Teile erstmals in Triebwerken einsetzen zu können.“
V.l.n.r.: Herstellung des UltraFan-Lufteinlassrahmens aus Thermoplast bei Daher; Airbus- und Daher-Teams gemeinsam im ersten Prototyp
Nach mehr als zwei Jahrzehnten erfolgreicher Arbeit auf dem Gebiet der Antriebstechnik bestätigt dieses Vorzeigeprojekt die Positionierung von Daher in drei wichtigen Bereichen: dem Umfeld des Pylons (RSS), dem Umfeld der Gondel (AIOS, akustische Schalen) und im heißen Umfeld der Triebwerke. In jedem dieser Bereiche konzentriert Daher seine Forschungs- und Entwicklungsanstrengungen auf Strukturteile mit hohem Mehrwert, die es den Triebwerksherstellern ermöglichen werden, ihre Leistung und Wettbewerbsfähigkeit bis 2030 zu verbessern.
„Für die Luftfahrtindustrie besteht die größte Herausforderung des nächsten Jahrzehnts darin, die Umweltprobleme zu bewältigen. Alle unsere Projekte sind Teil dieser Dynamik. Verbundwerkstoffe, insbesondere Thermoplaste, sind ein echter Wendepunkt in der Welt der Flugzeugstrukturen. Sie erlauben die Herstellung von leichteren und festeren Teilen als die bisher verwendeten Metalle, und das zu geringeren Kosten. Die Vorteile sind im Hinblick auf die Leistung und die Begrenzung der ökologischen Auswirkungen des Luftverkehrs erheblich. Dies ist der entscheidende Punkt für die Flugzeuge der Zukunft. Daher werden wir alles daran setzen, unsere Führungsposition bei diesen Technologien zu behaupten, die es der Luftfahrt ermöglichen, das doppelte Dilemma von Wettbewerbsfähigkeit und geringerer Umweltbelastung zu lösen.“
Dominique Bailly, Directeur R&D de Daher