Composites avancés pour l’aéronautique : comment Daher élargit le champ des possibles
26/11/2020
Organisée le 26 novembre sur le thème « Sommes-nous prêts à concevoir et fabriquer en maîtrisant notre impact environnemental ? », la e-journée technique du Sampe France permet à Daher de souligner une nouvelle fois son avance et la pertinence de sa stratégie de longue date dans le domaine des composites et procédés avancés pour de nouvelles applications aéronautiques plus performantes et éco-responsables.
Améliorer l’aérodynamisme et l’éco-efficience globale des avions commerciaux, c’est l’objectif du programme « Wing of tomorrow » d’Airbus visant à développer la prochaine génération d’aile pour avion monocouloir (New Single Aisle). Les enjeux sont multiples : réduction des délais de mise sur le marché, réduction des coûts, performances, réduction de la masse, cadences de production… En confiant à Daher, dans le cadre de ce projet majeur en termes de recherche et développement, la conception et de la réalisation d’un faux longeron en composite thermodurcissable et de cinq nervures thermoplastiques fortement chargées, Airbus entendait bénéficier d’une expertise unique développée au fil des ans grâce à un enchainement méthodique de projets de R&D.
« La livraison, courant 2020, de ces nervures – des pièces de structure fortement sollicitées à l’effort, de grande dimension et complexes, avec une épaisseur variable en fonction des zones – est l’aboutissement de la décision stratégique de Daher, il y a plus de dix ans, de concentrer l’effort de R&D accompagnant la transformation du Groupe sur la conception et la réalisation de pièces composites à plus forte valeur ajoutée, explique Dominique Bailly, Directeur R&D de Daher. En identifiant et en nous concentrant très vite sur deux axes prioritaires – la voilure et l’environnement moteur -, nous avons élaboré la feuille de route technologique qui nous permettrait de proposer à temps, à la bonne maturité et au bon coût des solutions compétitives et différenciantes répondant aux enjeux de l’industrie aéronautique. Nous commençons aujourd’hui à voir les fruits de nos efforts. »
Voilure : une démarche graduée pour gagner en maturité
Côté voilure, Daher cible trois catégories de pièces : les longerons équipés, les nervures et les caissons de torsion. Avec un atout maître : sa capacité d’avionneur qui lui permet de développer et de tester ses innovations sur ses propres avions – légers, de type aviation générale-, avant de les « escalader » sur des catégories d’avions supérieures.
La première réalisation d’importance est baptisée EcoWingbox, une grande voilure en composite carbone de 14 mètres de long développée entre 2009 et 2014 pour un projet d’avion Daher. Pour la cuisson de cette pièce de grande dimension, l’autoclave est remplacé par une étuve qui offre la même capacité de production pour un coût bien moindre. « Avec les dépenses d’investissement d’un autoclave, on peut disposer de 5 étuves et répondre ainsi à l’enjeu d’accélération des cadences de l’industrie aéronautique », souligne Dominique Bailly. Le procédé sera donc utilisé sur tous les projets qui vont suivre.
En 2017, Daher embarque avec Dassault sur le projet Corac « Avion du futur composite » dans le cadre duquel il conçoit et réalise une première nervure en thermoplastique ainsi qu’un longeron arrière entièrement en composite thermodurcissable hors autoclave. L’histoire continue donc et Daher monte progressivement en maturité sur la réalisation de pièces complexes en composites. « Des pièces plus grandes, plus sollicitées à l’effort, intégrant plus de fonctions, à l’épaisseur évolutive etc…, résume Dominique Bailly. Ce projet nous a aussi donné l’opportunité de concevoir, de réaliser et de tester à échelle réelle une première nervure en thermoplastique, le matériau clé de certaines aérostructures du futur qui permet de produire, à coût contenu et à forte cadence, des pièces plus légères mais aussi plus résistantes que les métaux employés précédemment. »
Dès lors, Daher est prêt à aller plus loin, à monter encore en difficulté. Son avance technologique lui permet d’intégrer courant 2019 l’ambitieux programme « Wing of tomorrow » d’Airbus au sein duquel il se voit confier la conception et de la réalisation de plusieurs pièces parmi les plus critiques et complexes du programme : un faux longeron arrière entièrement en composite thermodurcissable hors autoclave, ainsi que les cinq types de nervures en thermoplastique présentées à la e-journée technique 2020 du Sampe France.
« Nous sommes très fiers d’avoir répondu aux attentes très élevées d’Airbus sur ce projet et d’avoir été parmi les premiers à livrer nos réalisations. C’est une nouvelle preuve de notre maturité dans le domaine des composites avancés. Et de la pertinence de nos choix stratégiques : nous avions misé sur ces pièces clés de la voilure dès 2009 ! »
Daher ajoute aujourd’hui une nouvelle brique à son édifice : la soudure thermoplastique par induction – sans rivetage – qui permettra une significative réduction de poids et du temps d’assemblage des avions. « Là encore, nous nous appuyons sur notre avion de type aviation générale pour démontrer le bien-fondé de cette technologie et notre capacité à concevoir et certifier une pièce critique. Nous travaillons en R&D dans le cadre du projet Trampoline du Corac sur un exemple de caisson de torsion soudé du plan horizontal fixe de l’avion. Notre objectif de demain est de répandre cette technologie chez nos clients et partenaires, en allant, une fois nos conceptions validées, chercher des essais sur les parties mobiles de la voilure ou de l’empennage d’avions plus gros. Avec notre avion, nous disposons d’une « plateforme » d’expérimentation et de démonstration tout à fait unique en son genre, autour de laquelle nous avons structuré notre programme d’innovation en interne et dont nous pouvons faire bénéficier nos partenaires, et en particulier les autres avionneurs. Nous pouvons tester à petite échelle de nouvelles technologies, leur capacité à être certifiées… et ils peuvent ensuite imaginer un « scale-up » pour leurs propres programmes. Et cela vaut également pour les motoristes…»
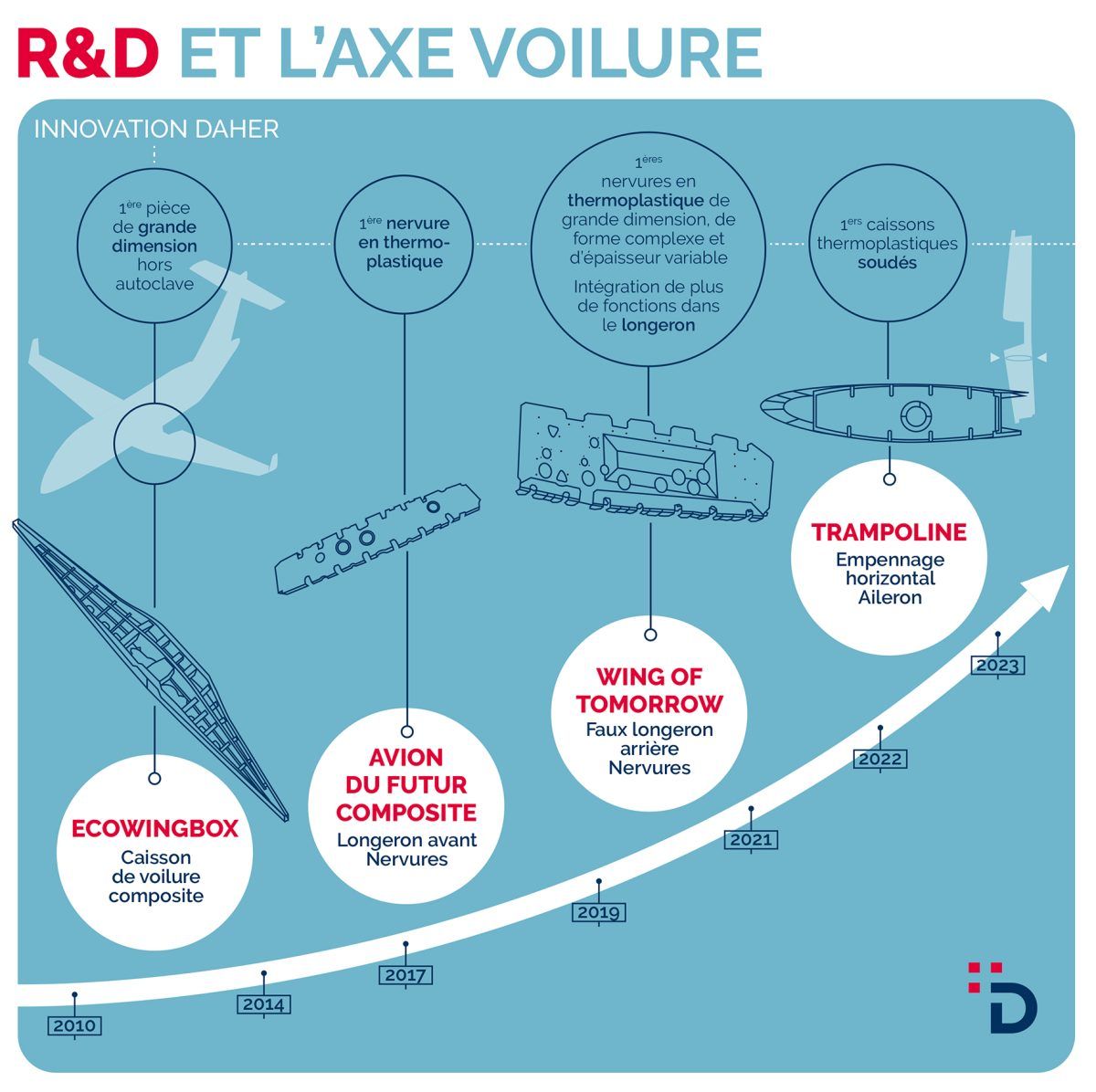
L’horizon s’élargit dans l’environnement moteur
La stratégie de Daher dans l’environnement moteur prend aujourd’hui un virage décisif avec la réalisation d’une première pièce structurale en thermoplastique : le cadre d’entrée d’air d’un démonstrateur du révolutionnaire moteur UltraFan de Rolls-Royce. Avec sa circonférence de plusieurs mètres, cette pièce, constituée de 4 sections assemblées, est l’une des plus grandes jamais réalisées en thermoplastique.
C’est à Airbus que Rolls-Royce a confié le développement des nacelles qui supporteront ce moteur nouvelle génération dont l’objectif est de réduire drastiquement la consommation de carburant (de l’ordre de -25%) et les nuisances sonores des avions long courrier. L’UltraFan sera le plus grand moteur d’avion du monde lors de son entrée en service vers la fin de la décennie. Le challenge pour Airbus est de parvenir à concevoir une nacelle aux dimensions inédites sans alourdir l’avion. Le recours massif aux nouveaux matériaux composites s’impose et le choix du tout thermoplastique pour le cadre d’entrée d’air est une première mondiale. Pour sa fabrication, Airbus se tourne naturellement vers Daher, déjà engagé à ses côtés dans le programme « Wing of tomorrow » et qui a déjà prouvé sa capacité de réalisation de pièces particulièrement complexes en thermoplastique.
« Airbus est responsable du design et du choix des matériaux mais nous nous sommes inscrits dans une vraie démarche de co-engineering avec eux pour que la pièce soit fabricable – et à coût maîtrisé – avec la technologie de placement de fibres automatisé (AFP) que nous sommes parmi les premiers à maîtriser au niveau adéquat, explique Alexandre Lambert, chef de projet R&D chez Daher. Le challenge était néanmoins considérable compte-tenu des caractéristiques de la pièce, à savoir sa grande taille, sa très faible épaisseur et sa forme conique et courbe… Une équation très complexe que nous avons cependant réussi à résoudre, conformément au cahier des charges d’Airbus. La pièce a été acceptée pour les essais mécaniques en vol prévus courant 2023. Pour Daher, c’est une grande fierté de pouvoir faire voler des pièces en thermoplastique dans l’environnement moteur. »
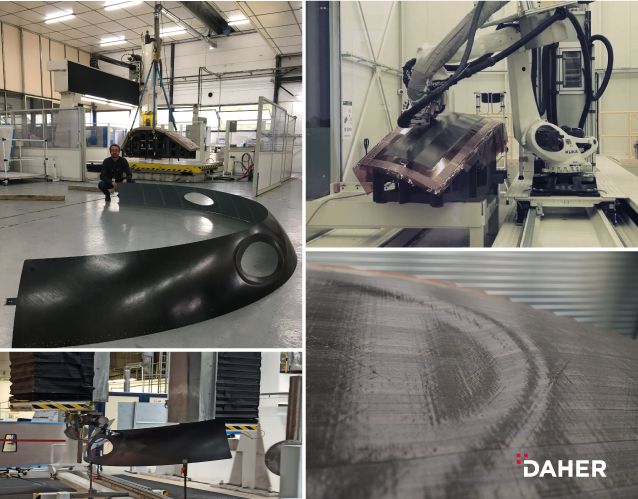
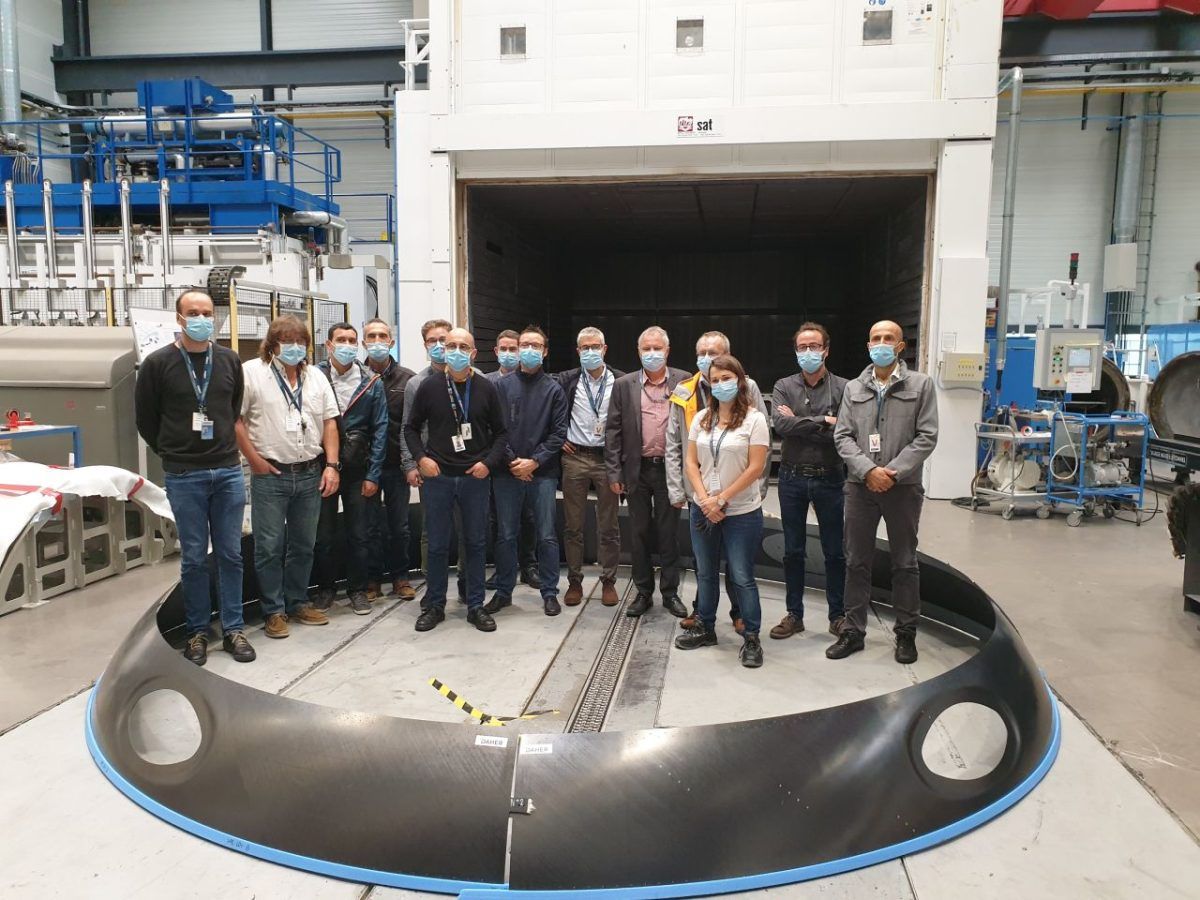
De g. à dr. : fabrication chez Daher du démonstrateur de cadre d’entrée d’air entièrement en thermoplastique de l’UltraFan ; les équipes Airbus et Daher réunies dans le premier démonstrateur
Après plus de deux décennies de réalisations dans le domaine de la propulsion, cette réalisation phare conforte le positionnement de Daher autour de trois axes majeurs : l’environnement pylône (RSS[1]), l’environnement nacelle (AIOS[2], viroles acoustiques) et l’environnement tiède des moteurs. Sur chacun de ces axes, Daher fait désormais porter son effort de recherche et développement sur des pièces structurales à forte valeur ajoutée qui permettront aux motoristes de gagner en performance et en compétitivité à l’horizon 2030.
« Pour l’aéronautique, le principal challenge de la décennie à venir est de parvenir à relever le défi environnemental. Tous nos projets s’inscrivent dans cette dynamique. Les composites, et en particulier le thermoplastique, sont de véritables game changers dans le monde des aérostructures. Ils permettent de produire, à coût contenu, des pièces plus légères mais aussi plus résistantes que les métaux employés précédemment. Les gains sont importants en termes de performances et de limitation de l’impact écologique du transport aérien. C’est le point clé des structures du futur. Daher fera tout pour maintenir son leadership sur ces technologies qui permettent à l’aviation de résoudre le double dilemme de la compétitivité et de la diminution de l’impact environnemental. »
Dominique Bailly, Directeur R&D de Daher
[1]RSS : Rear Secondary Structure
[2] AIOS : Air Inlet Outer Surface